P.O.L.A.R
High efficiency manufacturing of prosthetic sockets
Research Aims
-
Identify and develop advanced 3D printer designs to significantly increase the speed at which a viable, lower limb prosthetic socket can be manufactured.
-
Explore mateirals and manufacturing strategies to enhance the strength of 3D printed prosthetic sockets to a point where they can reliably pass ISO10328 testing.
-
Develop a logistical model sof distributed manufacturing of custom fitted prosthetic sockets in LMICs.
The Challenge
Millions of people worldwide, primarily in low and middle-income countries (LMICs), live with limb loss. Traditional prosthetic socket manufacturing is time-consuming, labor-intensive, and requires specialized skills. This creates a significant gap between the need for prosthetics and the availability of affordable, accessible solutions. While 3D printing offers potential, existing challenges such as slow print times and insufficient mechanical strength hinder its widespread adoption in LMICs.
The Solution
The POLAR 3D printer addresses these challenges by offering a rapid, cost-effective, and customizable solution for producing prosthetic sockets. Our innovative polar kinematics design significantly reduces print time compared to traditional Cartesian printers. By employing dual print heads and advanced materials, we aim to achieve the required mechanical strength while maintaining high production speed [1].
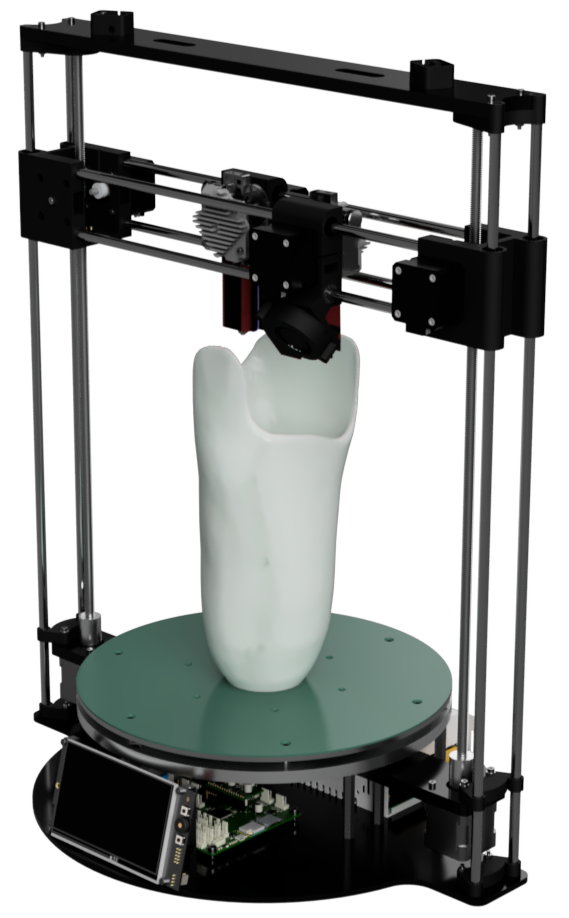
Our Approach
We have developed a prototype polar 3D printer optimized for socket production. Key features include:
- Polar kinematics: Enables faster circular motion, ideal for cylindrical socket shapes.
- Dual print heads: Increase material deposition rate and allow for composite materials.
- Advanced materials: Support for high-performance materials like PEEK and nylon to enhance strength.
- Custom slicing software: Optimizes toolpaths for the polar printer, ensuring precise and efficient production.
Impact
Initial simulations demonstrate a dramatic reduction in print time compared to existing 3D printers. We are currently refining our prototype and conducting rigorous testing to evaluate print times, mechanical strength, and overall performance. Successful development of the POLAR 3D printer has the potential to revolutionize prosthetic care in LMICs by providing a scalable, affordable, and efficient solution for producing personalized prosthetic sockets.
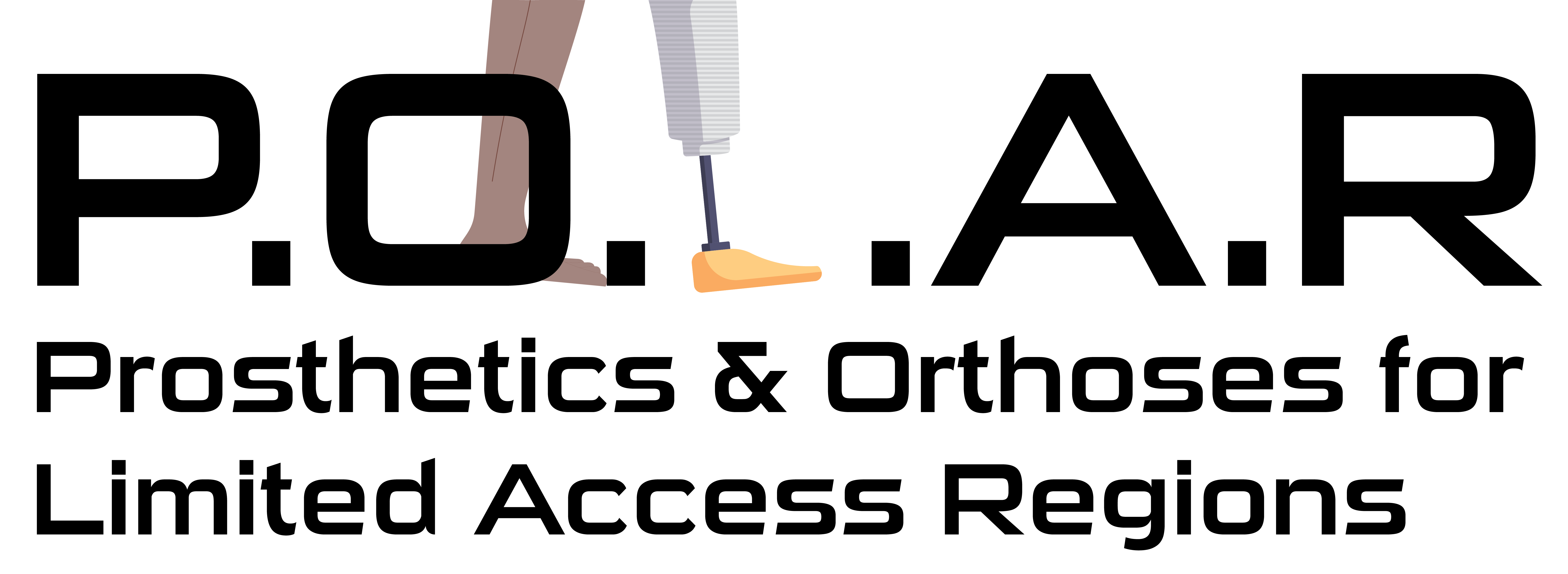
Collaborators
- Dr Angus B. Clark, Imperial College London
- Dr Buki Omarali, Imperial College London
Funding
- Imperial College London